Recommendations for safer installation and fixing of safes are as follows:
1. Before the safe is installed and fixed, remove the machine feet at the bottom of the safe box and the casters at the bottom of the safe, so that there is no gap at the bottom after the safe and the cabinet are installed and fixed, which is more effective to prevent the safe and the cabinet from being moved.
2. The safe must be installed and fixed on the concrete wall, and professional personnel are responsible for the installation to ensure the strength and quality of the installation and fixation.
3. Choose a suitable and hidden location to install and fix safes and cabinets, and install and fix the left and back of the safes and cabinets against the wall at the same time, which has better anti-prying and anti-theft effects. If you can make furniture cover up outside the safe and cabinet, it will be better to protect the privacy and security of the safe and cabinet.
Production process
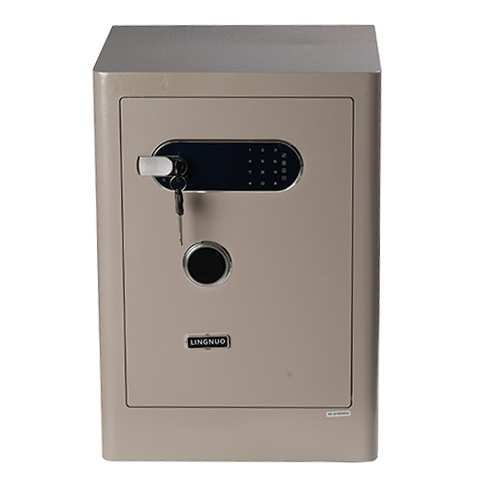
The general process of making a safe:
Sheet metal blanking---> Sheet metal forming---> Welding processing--->Surface treatment--->Assembly--->General inspection--->Packing--->Storage
From the above table, we may not have a clear understanding of the production process of the safe. Let us understand the meaning of each process in detail, so that we can deeply understand the production process of the safe:
Steel plate blanking: As we all know, the raw material of the safe is made of steel plate. Our first process is to pass the purchased large steel plates through the shearing machine and cut them into small plates that we need to facilitate the processing in the next process. This is like making clothes. Cut the cloth into small squares for collars, cuffs, etc.
Sheet metal forming: pass the small plates through various punching machines, dies, bending machines and other machinery and equipment to process various components required for the safe, such as: door panels, back panels of the box, bottom plates, and various mechanisms. For example, when making clothes, the small square cloth is cut into various preliminary shapes such as collars and cuffs.
Welding processing: The various formed sheets are welded to form a box with a door. Through such a process, the preliminary framework of the safe has been basically established. Similar to making clothes, various shaped materials are sewn together through a sewing machine to form basic shaped clothes.
Surface treatment: through various processes, the blank of the safe is refined and processed, and finally the entire process of spraying the surface of the safe is carried out. Since the safe after welding is relatively rough, we need to polish and remove the slag. Since there are rust spots and oil stains on the surface of the safe, phosphating treatment is required to achieve the purpose of
Custom hotel safe suppliers removing oil and rust. Because the surface of the safe blank is relatively rough, Therefore, putty ash should be scraped on the surface like furniture, and polished smooth, and finally high-temperature electrostatic spraying treatment is performed to form paint on the surface. The process is similar to ironing a sewn garment and trimming off any excess stitches.
Assembly: Assembly is the process of combining various elements such as locks and accessories that make up the safe to form a complete and usable safe. If the lock uses an electronic combination lock, it is called an electronic safe; if the lock uses a mechanical lock, it is called a mechanical safe; if a fingerprint lock is used, it is called a fingerprint safe. There are many accessories assembled, mainly including casters, locks (door locks, emergency locks, password locks), operation panels, mechanisms (including door bolts, handles, etc.), back covers, accessories (drawers, flannel, stickers, manuals) , partitions, etc.). Just like the final assembly process of making clothes, you need to nail buttons, mark the logo on the clothes and so on.
General inspection: The general inspection is to check the quality process of the safe, whether the produced safe meets the requirements of the company's original design, whether there are various missing accessories, whether the paint meets the standard requirements, whether it is flexible in use, and whether the anti-theft performance is not. compliance, etc. This process is very important. If the problem of the safe is not checked out, it will flow into the market and cause losses and customer complaints. The general inspection mentioned here is the final inspection of the whole project. In fact, the safe needs to be inspected for each process link in the production process. This is called process inspection. The accessories processed by external cooperation also need to be inspected, which is called external cooperation. test. In short, the general inspection is one of the important means to control the quality.
Packaging and warehousing: This process is the last process in the production of safes. The safes that have passed the inspection are packaged to meet the needs of transportation and storage. This link is also a very important process. Many safes in the market have paint bumps. Injuries and accessories are often damaged due to unreasonable packaging and transportation. Therefore, even at the sales terminal, special care must be taken for the transportation, loading and unloading of products, and the selection of warehouses should fully consider ventilation, drying, and anti-leakage and rain, so as to prevent products from being damp and damaged.